SiMDA-MES设备管理模块故障预警原理_珠海盈致
2025-03-14
一、MES设备管理模块故障预警体系架构
SiMDA-MES设备管理模块的故障预警体系由数据采集层、模型构建层、预警执行层三大核心层级构成,形成“感知-分析-决策”闭环。通过工业物联网(IIoT)技术,系统实时采集设备运行参数(如振动、温度、电流等)、工艺数据(加工速度、能耗)及环境信息(温湿度、粉尘浓度),并依托边缘计算节点进行数据清洗与特征提取,为后续分析奠定基础。
在MES设备管理框架中,设备联网率可达98%以上1,数据颗粒度精确至毫秒级,为精准预警提供底层支持。例如,某汽车零部件企业通过部署2000+传感器,日均采集数据量超10亿条,故障识别响应时间缩短至30秒内。
二、多维度数据分析与故障特征建模原理
1. 设备健康状态基线建模
系统基于历史运行数据构建设备健康状态基线,采用动态时间规整(DTW)算法和相似性原理(SBM),对设备振动频谱、能耗曲线等关键指标进行模式匹配。当实时数据偏离基线阈值15%时触发初级预警,并结合设备劣化趋势预测剩余寿命。
2. 机器学习驱动的故障预测
通过集成随机森林、LSTM神经网络等算法,MES设备管理模块实现故障类型的智能分类与概率预测。以数控机床为例,系统可识别主轴轴承磨损(准确率92%)、刀具断裂(准确率89%)等6类常见故障,并提前3-48小时发出预警,避免非计划停机。
3. 多源数据融合分析
系统将设备运行数据与生产计划、维护记录等业务数据关联,建立复合型故障预警模型。例如,结合设备负载率与生产排程数据,预测高负荷时段可能出现的过载故障;或关联备件库存数据,自动生成预防性维护建议。
三、预警触发与执行机制
1. 分级预警策略
根据故障影响程度设置四级预警机制:
--提示级(参数轻微波动):通过MES设备管理看板推送消息
--警告级(性能下降10-30%):触发声光报警并生成工单
--紧急级(可能引发停机):自动暂停设备并通知责任人
预警事件自动触发“诊断-派工-修复-验证”闭环流程:
--系统推送故障诊断报告(含可能原因和解决方案)至移动终端
--基于地理位置和技能标签智能派发工单
--维修人员通过AR眼镜查看设备三维拆解图与维修指引
--修复后系统自动复检参数,更新设备健康档案
四、技术优势与应用成效
通过某半导体企业实测数据对比,部署MES设备管理模块后:
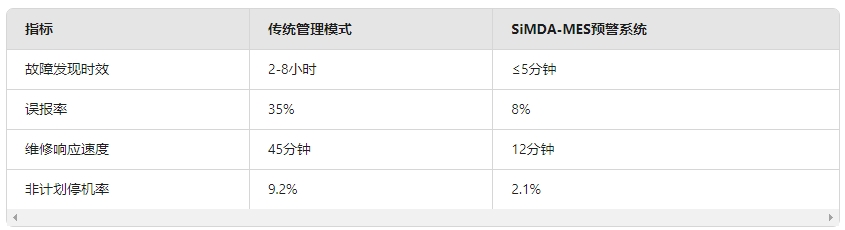
该系统通过设备OEE(综合效率)分析,帮助企业提升设备利用率23%,年节省维护成本超200万元。在食品加工、新能源等连续生产行业,预警准确率可达91%,有效避免批次性质量事故。
五、发展趋势与创新方向
未来MES设备管理模块将向数字孪生融合方向发展:
1.虚拟调试预警:在数字孪生体中模拟设备运行,预判物理设备的潜在故障
2.区块链存证:将预警事件、处理过程加密上链,满足合规审计需求
3.能耗-故障关联模型:通过分析设备能效曲线,识别异常用电背后的机械故障
珠海盈致建议企业依托模块化设计,将故障预警与生产排程、质量追溯等模块联动,逐步实现从“被动响应”到“预测性维护”的智能化转型。未来,该模块将融合数字孪生与能耗关联模型,进一步强化故障预演与能效优化能力],为智能制造提供更可靠的设备保障。
SiMDA-MES设备管理模块的故障预警体系由数据采集层、模型构建层、预警执行层三大核心层级构成,形成“感知-分析-决策”闭环。通过工业物联网(IIoT)技术,系统实时采集设备运行参数(如振动、温度、电流等)、工艺数据(加工速度、能耗)及环境信息(温湿度、粉尘浓度),并依托边缘计算节点进行数据清洗与特征提取,为后续分析奠定基础。
在MES设备管理框架中,设备联网率可达98%以上1,数据颗粒度精确至毫秒级,为精准预警提供底层支持。例如,某汽车零部件企业通过部署2000+传感器,日均采集数据量超10亿条,故障识别响应时间缩短至30秒内。
二、多维度数据分析与故障特征建模原理
1. 设备健康状态基线建模
系统基于历史运行数据构建设备健康状态基线,采用动态时间规整(DTW)算法和相似性原理(SBM),对设备振动频谱、能耗曲线等关键指标进行模式匹配。当实时数据偏离基线阈值15%时触发初级预警,并结合设备劣化趋势预测剩余寿命。
2. 机器学习驱动的故障预测
通过集成随机森林、LSTM神经网络等算法,MES设备管理模块实现故障类型的智能分类与概率预测。以数控机床为例,系统可识别主轴轴承磨损(准确率92%)、刀具断裂(准确率89%)等6类常见故障,并提前3-48小时发出预警,避免非计划停机。
3. 多源数据融合分析
系统将设备运行数据与生产计划、维护记录等业务数据关联,建立复合型故障预警模型。例如,结合设备负载率与生产排程数据,预测高负荷时段可能出现的过载故障;或关联备件库存数据,自动生成预防性维护建议。
三、预警触发与执行机制
1. 分级预警策略
根据故障影响程度设置四级预警机制:
--提示级(参数轻微波动):通过MES设备管理看板推送消息
--警告级(性能下降10-30%):触发声光报警并生成工单
--紧急级(可能引发停机):自动暂停设备并通知责任人
--灾难级(存在安全风险):联动PLC执行紧急停机
预警事件自动触发“诊断-派工-修复-验证”闭环流程:
--系统推送故障诊断报告(含可能原因和解决方案)至移动终端
--基于地理位置和技能标签智能派发工单
--维修人员通过AR眼镜查看设备三维拆解图与维修指引
--修复后系统自动复检参数,更新设备健康档案
四、技术优势与应用成效
通过某半导体企业实测数据对比,部署MES设备管理模块后:
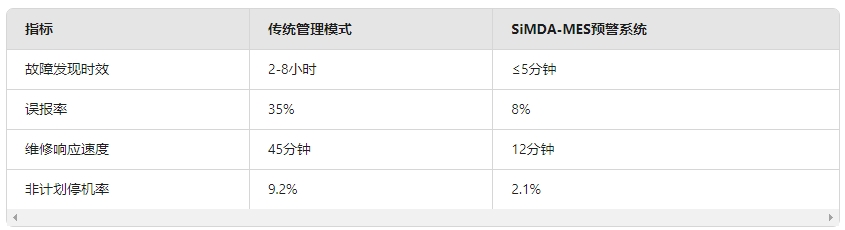
该系统通过设备OEE(综合效率)分析,帮助企业提升设备利用率23%,年节省维护成本超200万元。在食品加工、新能源等连续生产行业,预警准确率可达91%,有效避免批次性质量事故。
五、发展趋势与创新方向
未来MES设备管理模块将向数字孪生融合方向发展:
1.虚拟调试预警:在数字孪生体中模拟设备运行,预判物理设备的潜在故障
2.区块链存证:将预警事件、处理过程加密上链,满足合规审计需求
3.能耗-故障关联模型:通过分析设备能效曲线,识别异常用电背后的机械故障
珠海盈致建议企业依托模块化设计,将故障预警与生产排程、质量追溯等模块联动,逐步实现从“被动响应”到“预测性维护”的智能化转型。未来,该模块将融合数字孪生与能耗关联模型,进一步强化故障预演与能效优化能力],为智能制造提供更可靠的设备保障。