MES系统防错:智能制造时代的质量守护者
2025-04-07
作为连接企业计划层与控制层的中枢,MES(制造执行系统)通过实时监控、数据追溯、智能校验三大核心能力,构筑起生产过程的“防呆防错”屏障。以珠海盈致科技有限公司为代表的解决方案提供商,正通过创新技术助力企业实现从“事后纠错”到“过程防控”的质控跃迁。
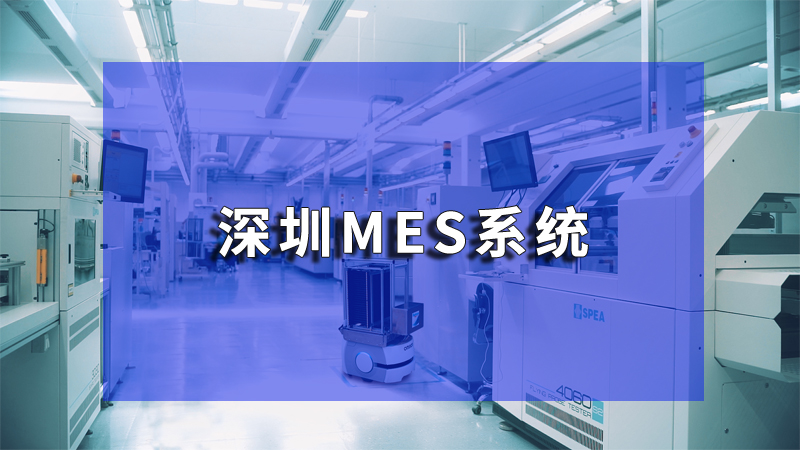
一、MES系统防错的技术逻辑
MES系统防错的本质是通过数据驱动实现全流程闭环管理,其技术架构包含三个层级:
感知层:依托RFID、机器视觉、IoT传感器等设备实时采集生产数据,例如珠海盈致为某汽车零部件厂商部署的视觉检测系统,可0.2秒内识别零件装配误差;
分析层:通过规则引擎与机器学习模型,对物料批次、工艺参数、设备状态进行交叉验证。当检测到BOM清单与工单不匹配时,系统将自动锁定生产线并推送预警;
执行层:联动PLC控制系统实现自动纠偏,如在电子贴片工序中,系统可实时调整贴装压力参数,避免因压力偏差导致的虚焊问题。
二、防错机制的四大核心场景
在珠海盈致服务的300余家制造企业中,MES系统防错主要聚焦以下场景:
1. 物料防呆
通过“三码联动”校验机制(工单码+物料码+设备码),确保生产投料的绝对准确性。某家电企业实施该系统后,错料事故下降92%,年节约成本超800万元。系统内置的批次追溯功能可精确到分钟级定位问题源头,例如当某批电路板出现焊接不良时,10分钟内即可追溯至锡膏供应商的工艺参数异常。
2. 工艺防错
基于SPC(统计过程控制)的动态监测模型,系统可识别0.1%的工艺参数偏移。珠海盈致为某光伏企业设计的硅片切割方案,通过实时分析切割速度、金刚线张力等18项参数,将碎片率从1.2%降至0.3%。对于关键工序,系统还设置硬校验节点,例如汽车总装线必须完成扭矩校验方可进入下一工位。
3. 设备防漏
通过设备健康度预测模型,提前48小时预警潜在故障。某精密机械制造商接入该功能后,设备非计划停机时间减少75%。系统还能自动比对设备点检记录,若发现润滑周期超期未执行,将冻结设备启动权限。
4. 人员防误
电子作业指导书(ESOP)与增强现实(AR)技术的结合,让操作员通过智能眼镜接收实时指引。在珠海盈致参与的某航空装备项目中,AR导航使复杂装配的错误率降低80%,培训周期缩短60%。
三、技术演进:从规则防错到认知防错
当前MES系统防错技术正经历三大升级:
多模态融合:整合视觉、声纹、红外等多维度数据,例如通过声学传感器识别数控机床的异常振动频谱;
自适应学习:基于历史缺陷数据的深度学习模型,可自主优化检测阈值。某半导体企业验证显示,系统误报率每月递减15%;
预测性防控:通过数字孪生技术模拟生产波动,提前生成风险预案。当预测到注塑机模温即将超标时,系统可自主调节冷却水流量。
四、实施路径:构建防错体系的四个关键
标准化梳理:建立覆盖328项工艺控制点的企业防错知识库,将专家经验转化为数字化规则;
渐进式部署:优先在质检、仓储等关键环节部署防错模块,逐步向全流程扩展;
人机协同设计:保留关键岗位的人工复验节点,避免过度依赖系统导致的认知退化;
持续优化机制:每月分析防错日志,通过PDCA循环迭代规则库。某医疗器械企业通过该机制,使防错规则的有效性从76%提升至94%。
五、未来展望:防错技术的价值延伸
随着5G+工业互联网的深度融合,MES系统防错正在突破生产边界:
供应链联防:珠海盈致正在测试的产业协同平台,可将防错规则延伸至供应商端,实时校验来料质量;
碳效管理:通过分析设备能耗与工艺合格率的关联数据,优化生产排程降低碳足迹;
客户定制:在个性化订单生产中,系统自动校验客户定制参数与产线兼容性,避免设计缺陷流入制造环节。